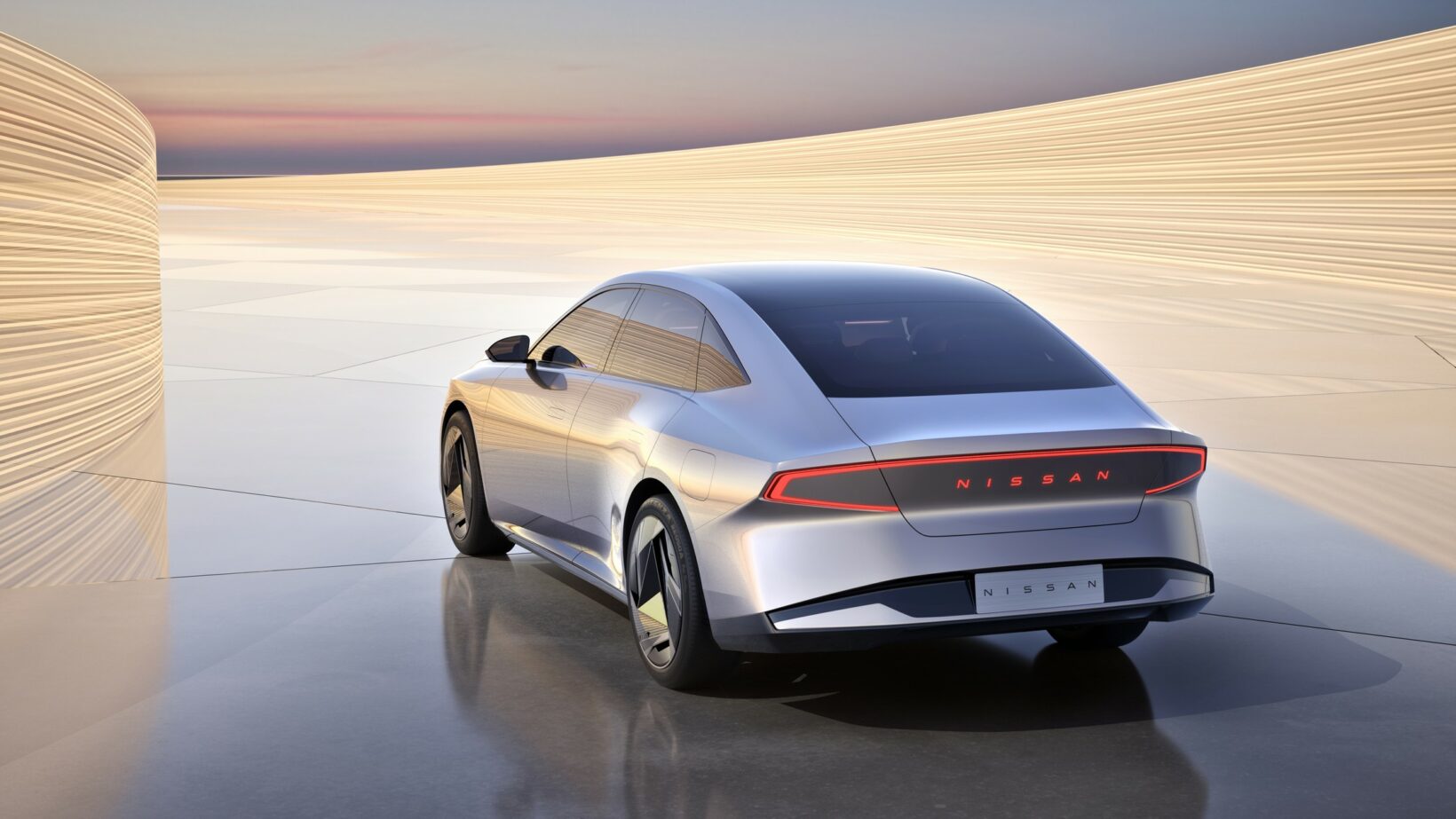
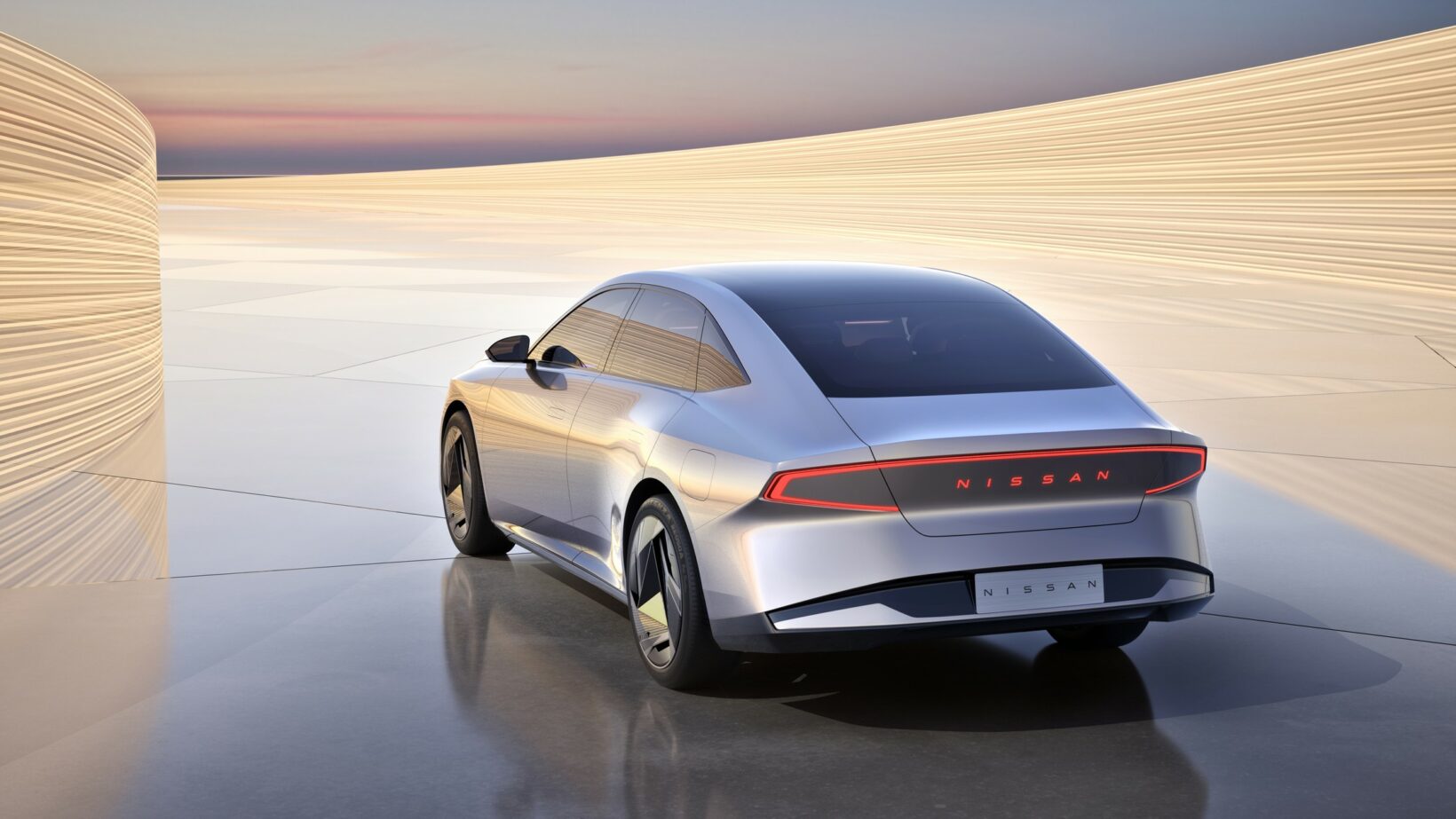
Nissan is implementing a new way to industrialize its production and reduce costs. Through large hydraulic presses, the manufacturer aims to reduce the number of parts in its cars.
Nissan’s decision is further evidence of Tesla’s influence on the automotive market. The Japanese automaker will use hydraulic presses to manufacture chassis in one piece.
Specifically, certain parts of the chassis will be made in one piece, as seen in the Model Y and Cybertruck. Other brands like Hyundai and Ford are also working on this technology.
According to Automotive News, Nissan’s goal is to reduce the costs of electric vehicles. The cost of parts is expected to decrease by 10%, and the weight is projected to drop by about 20%.
Nissan aims to have these large hydraulic presses ready by 2027. The total production cost is expected to decrease by 30%, resulting in savings of $1 billion.
Similar to Tesla, the rear and lower part of the chassis will be manufactured using this process. This allows for the consolidation of around a hundred parts into a single piece, which will be molded in the hydraulic press.
The drawback of this technology is the cost of the machine itself, which must be recouped before starting to make a profit. Additionally, vehicles made of a single large piece in the rear are more challenging to repair.
In addition to the above information, it is worth noting that the use of hydraulic presses by Nissan demonstrates a significant shift towards more efficient and cost-effective manufacturing processes in the automotive industry. Companies like Tesla have set a precedent with their innovative approaches, encouraging other manufacturers to explore similar technologies for improving production efficiency and reducing costs in the production of electric vehicles. This shift towards more streamlined manufacturing processes not only benefits the companies in terms of cost savings but also contributes to the overall sustainability and competitiveness of the electric vehicle market.